Unfortunately, the situation is familiar to many: a machine that is well doing the job but has been in service for a long time needs a spare part that is no longer available. There is no time to waste; production stands still or suffers. Metal printing provides a quick solution and, at the same time, offers the opportunity to make clear improvements to an existing solution.
The short story above is similar to the situation with Konecranes, which has a highly competent and solution-oriented maintenance organisation. When a brake assembly for a crane conveyor reel, once purchased as a complete unit, lost a gear over the years, neither a spare part nor the drawings were available. In this case, the machining would have been tricky and time-consuming, even with an existing model. The solution was sought from Delva, a metal 3D printing service bureau. The work got off to a flying start. Delva scanned the defective gear and used the result to reverse engineer and model the component as a digital spare part.
When modelling existing components, it is always worthwhile to consider their optimisation potential. Although the existing solution is likely to limit the scope for change, optimisation can bring clear functional benefits and reduce the cost of printing. Eetu Kivirasi, an AM specialist at Delva, emphasises the importance of the interaction between the customer and the design engineering. Kivirasi knows that the range of potential operational challenges is vast, and the customer understands them best. This exchange of information lays the foundation for a successful design. A DfAM (Design for Additive Manufacturing) skilled designer will automatically take care of optimising the printability of the part, and the 3D printing service bureau will figure out the rest.
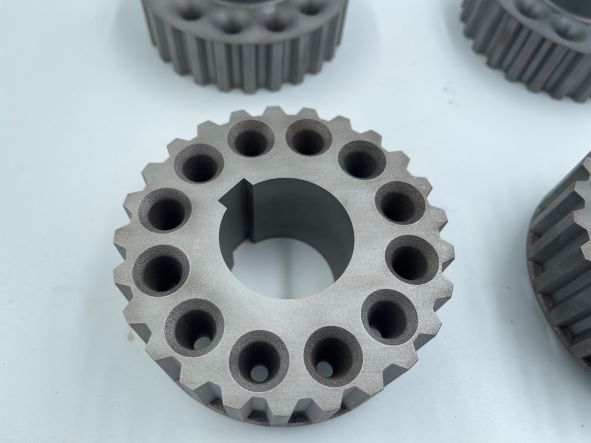
In the case of Konecranes, the gear was lightened to remove weight and reduce the cost of the implementation. The lighter solution will put less load on the bearing in use, so some of the benefits will be realised over time. In addition, the original separate rubber support mounted on the wheel could be eliminated by designing a closed gear ring. This adequately prevents the brake discs from falling off, resulting in an optimised component.
The choice of printing material is important
Successful print material selection is a critical factor in the 3D printing of spare parts. In many cases, the original material is not known with certainty. The material may also have been subject to wear or breakage in service. Even if the material is known and considered good, it is possibly not printable.
We have written a guide on material selection, which you can read here.
The key is to start with the desired performance of the component and the environmental conditions. Finally, the most economically viable material is selected from those that meet the criteria. The performance of the printed material is equivalent to that of a conventionally produced material. Components printed by controlled processes from high-quality materials with optimised parameters are of uniform quality and meet the promised performance. You can read about these on our website, where you can also download material-specific datasheets. MS1 tool steel was chosen for the Konecranes wheels. It is a high-strength material and increases the solution’s wear resistance.
As often said, prints can be machined, joined, and surface treated just like conventional components. However, each step that is eliminated saves time, money and logistics. In our case study, the manufacturing process was relatively brief: the parts were printed and heat-treated. The wheel was wire cut from the printing plate, and the axle hole was wire cut to size. In this case, printed teeth’ accuracy and surface quality were satisfactory. The result is delightful; you can see it in the pictures above and below.
Extend the life of machinery and equipment
It is essential that any industry seeking true sustainability in its business, regardless of the sector, strives to extend the life of its machinery and equipment. Maintenance and repair, as well as active efforts to improve processes to be energy efficient and minimise waste, are an important part of this effort.
Metal 3D printing is already seen as an opportunity by many companies and welcome addition to their toolbox. We encourage your company to get going, experiment and realise.
We at Delva are there to support you where you need it.
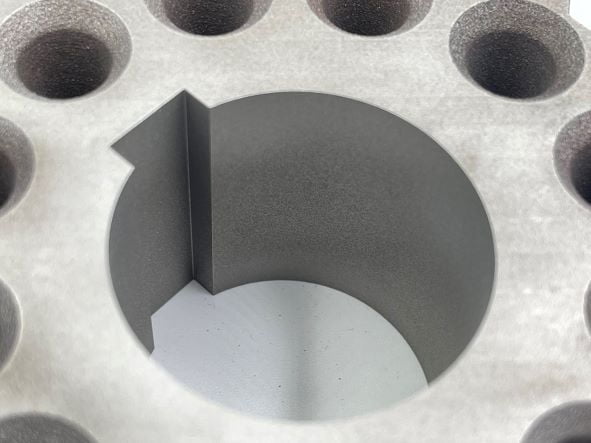