Copper for Metal 3D Printing
+
Apply copper to critical thermal transfer applications. The excellent thermal and electrical conductivity make copper an exciting material for various industrial applications.
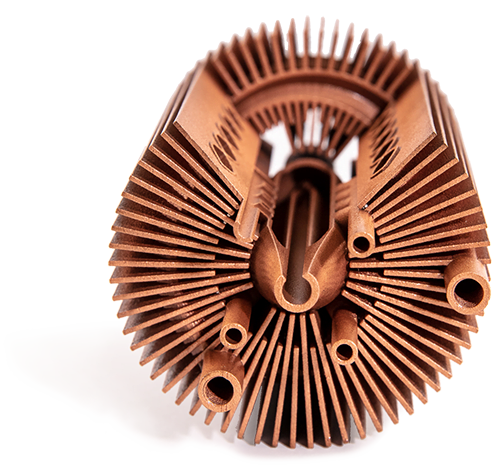
Copper
Metal 3D printing is the future of thermal management. Additively manufactured parts enable never-before-seen geometries for thermal management systems. Thus, improving both functionality and heat transfer with the total freedom of geometric shape.
Apply copper to critical thermal transfer applications. The excellent thermal and electrical conductivity make copper an exciting material for various industrial applications. For example, copper’s material characteristics make it ideal for heat exchangers, induction coils, electronics, components for electrical contact technology, as well as any application requiring maximised conductivity. Even rocket engine parts have been 3D printed from copper.
Typical applications:

Electrical motors

Inductors

Variety of industry applications requiring excellent conductivity properties
Main Characteristics:

Commercially pure copper (> 99.95% purity)

Excellent electrical and heat conductivity
Typical Part Properties
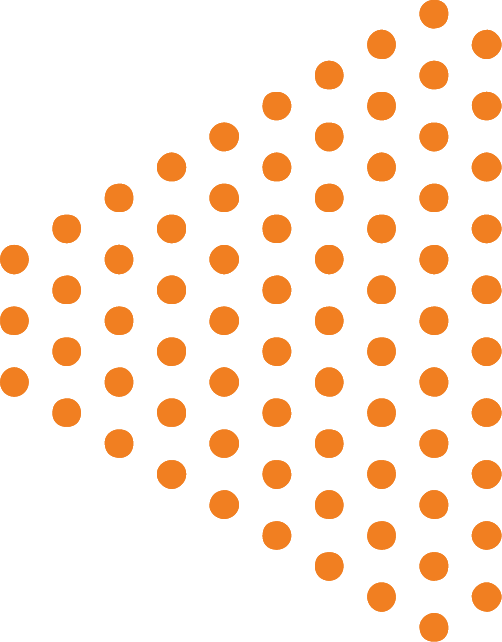
Delva uses metal powders that are designed and tested for use on EOS’ metal 3D printers. All EOS metal powders are shipped with an inspection certificate (according to EN 10204, Type 3.1) showing the results of the extensive QA testing not only of the powder itself, but also of test parts built on a dedicated system with a dedicated process.
Metal 3D printing Copper
At Delva, we use EOS copper powder, either 99.9% copper or high-purity (99.95%) copper.
There are several benefits 3D Printing copper has. First, performance increases through design optimisation that enables the implementation of non-linear and tapered geometries in extended structures like fins, vane blades, capillary wicking structures, heat pipes, and conformal internal passages. Secondly, the freedom of shape also enables part consolidation that makes it possible to gain savings in time, money, parts production, and assembly – without forgetting significant possibilities to realise weight and space savings in components designed and engineered for AM.
Production of heat exchangers with complex geometry based on traditional methods is challenging and time-consuming. With AM, we build the components by adding material only where it is needed to achieve optimised, lightweight, yet complex parts.
At Delva, we use a validated process for printing that offers an optimal combination of parameters (e.g. laser power, layer thickness, etc.) to ensure that we consistently achieve the properties of the 3D printed parts.