To boost success stories enabled by metal 3D printing, members of FAME (Finnish Additive Manufacturing Ecosystem) actively seek information and understanding. Delva has had the pleasure to host metal printing days on its premises in Hämeenlinna. In the following, we reflect on the benefits that hands-on learning offers for companies on their additive manufacturing journey.
Paraphrasing an old, good proverb, keeping the same means you get the same results. If we want new developments, we need to do things differently. There are plenty of examples showing that it is worthwhile looking for alternatives. By metal 3D printing, we build solutions that were not possible before. In addition to money and time savings, we support sustainable development by reducing material and energy usage throughout the lifecycle.
It is rewarding to learn new, and we are learning by doing. But the change challenges our thinking and practices. To imbed new thinking, companies need to allocate sufficient resources.
Metal 3D printing hands-on
A comprehensive understanding is beneficial whether the company wants to 3D print or get 3D printed. A foresighted company recognises the requirements of the transformation process and offers its personnel a possibility to a positive learning pathway and achievement experience. This kind of proceeding supports the motivation and creates an encouraging atmosphere. We can succeed in many ways. We at Delva believe in experiments and learning by doing.
Success in metal 3D printing does not come simply by starting a printer. Engineers create a significant part of the positive result on the design table, and no one is born a master. Instead of paying big money for backfired prototyping or hastily abandoning technology offering create opportunities, we can build success in good time by learning in practice. We believe that experimenting, communicating, and familiarising with various examples make a golden insight and help take a great leap towards utilising metal printing to achieve new, innovative solutions.
Cooperation is strength – also in metal printing
Metal 3D printing covers several different technologies. Powder Bed Fusion technology (PBF) is the most mature technology suitable for the most demanding applications, and it is already a manufacturing technology among conventional ones. Laser Powder Bed Fusion (L-PBF) is Delva´s choice.
3D printing with L-PBF, compared to conventional manufacturing, reduces work stages but still includes many things to do. Different tasks in the printing process like adequate nesting of build plates, printer cleaning, demanding handling of powders, not to mention part building in the printer, heat treatment, sawing and multiple post-processing are discovered best by doing.
We at Delva believe in cooperation and co-development. We can go a long way by joining customers´ profound knowledge of the industry in question and our knowledge and experience as a printing partner bureau of all the possibilities – and restrictions – of metal printing. Understanding each other’s work and possible challenges improves communication and help to find solutions together. Learning happens in interaction.
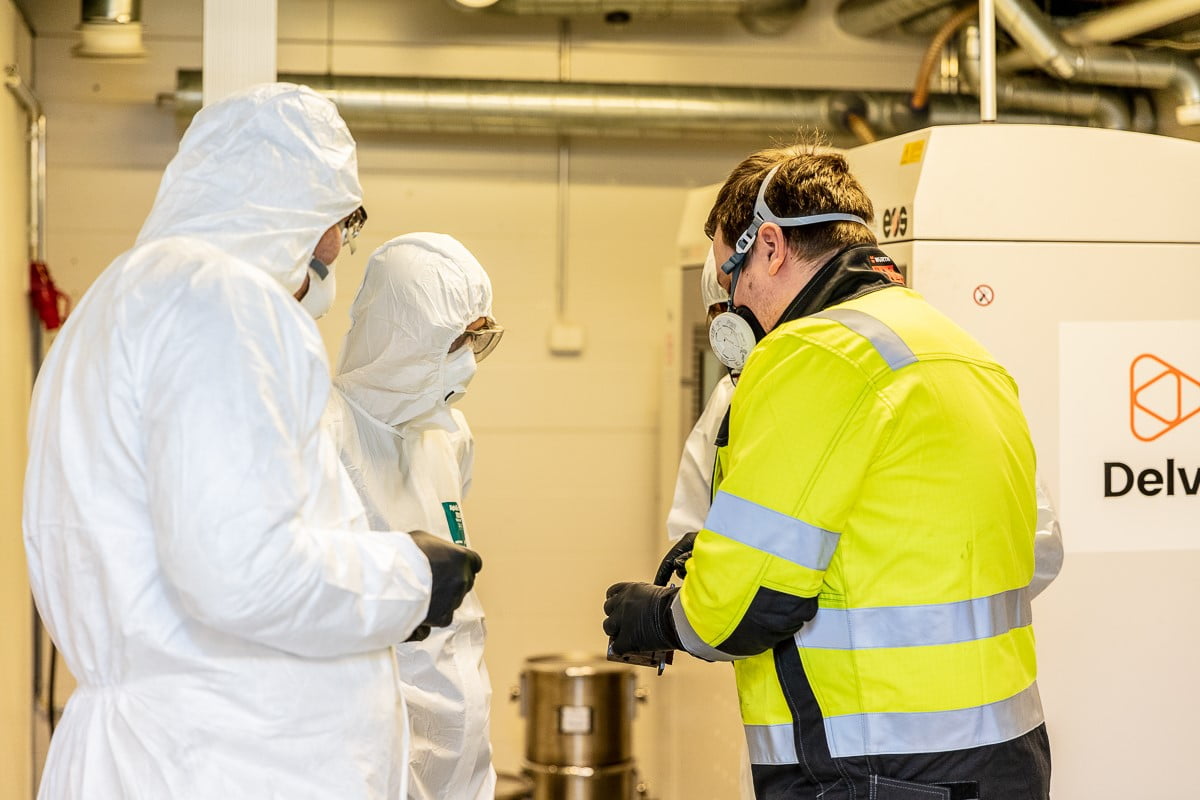
Picture: AM-specialist Eetu Kivirasi and Fame-members in interaction.
Support structures
Support structures have a significant role in metal printing. One basic rule is that the build tends to drop as the angle of an unsupported feature gets below 45 degrees. On earlier occasions, we have show-cased so-called support free low angles, where this 45-degree thumb of rule is challenged, and angles of even 13 degrees have been built. That is doable but always requires material-specific developments. A simple solution is to add support structures that help produce the wanted design. Support structures, however, increase the printed material and, this way, cost. In addition, supports need to be removed, depending on the material, either manually or by machining.
It is good to plan the manufacturing process minimising the support structures and considering removing those during the design phase. The necessity is concretised in a new way while removing support manually from a heat-treated 316L part. The experience springs to mind a long time.
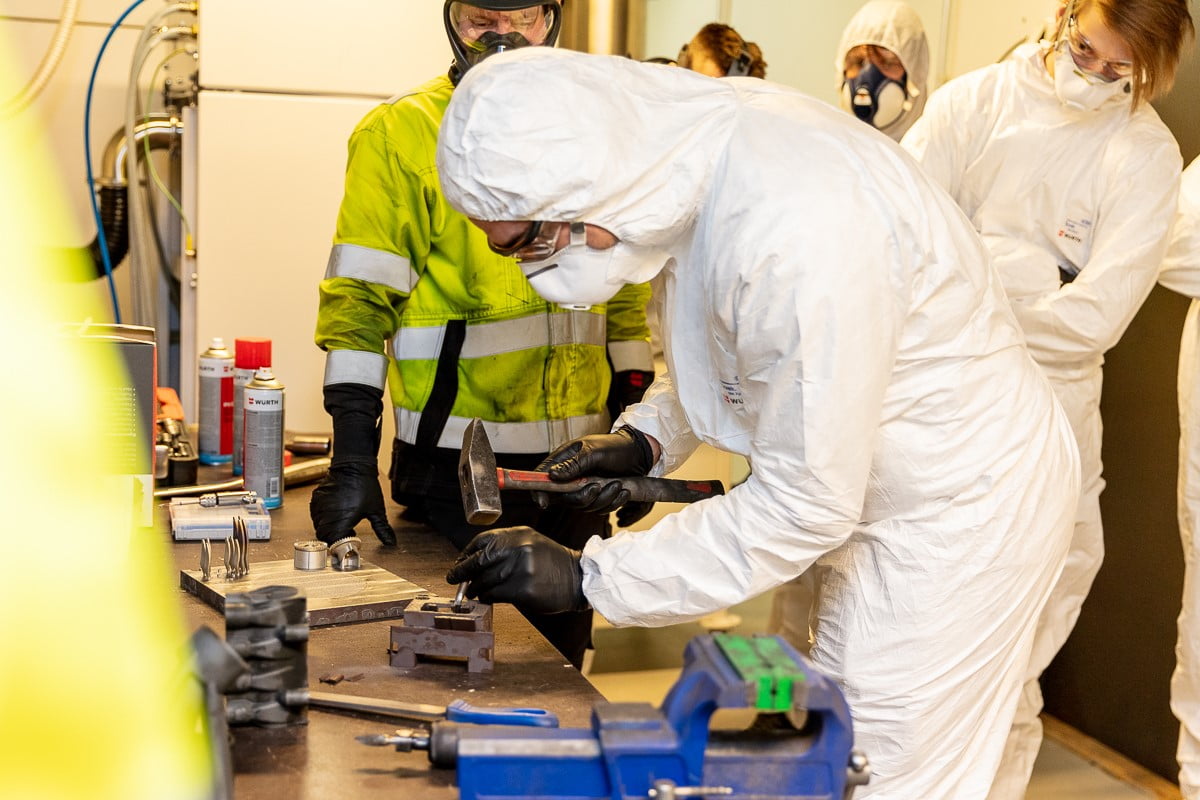
Picture: Removing support manually.
The law of conservation of powder
It is also good to learn that in powder bed fusion, the non-melted powder remains among the build in the building chamber until we vacuum-clean it at the end of the printing process. One of the significant advantages of metal 3D printing is producing lightened, even fully hollow structures. One must keep in mind that the powder stays inside the hollow structure, too, and it is essential to plan how to remove it in advance. It is annoying to use a long time to shake manually powder out of a part, otherwise costing a few euros or even finding out that the powder is stuck inside the structure forever. Applications also exist where powder residuals are critical and need to be excluded.
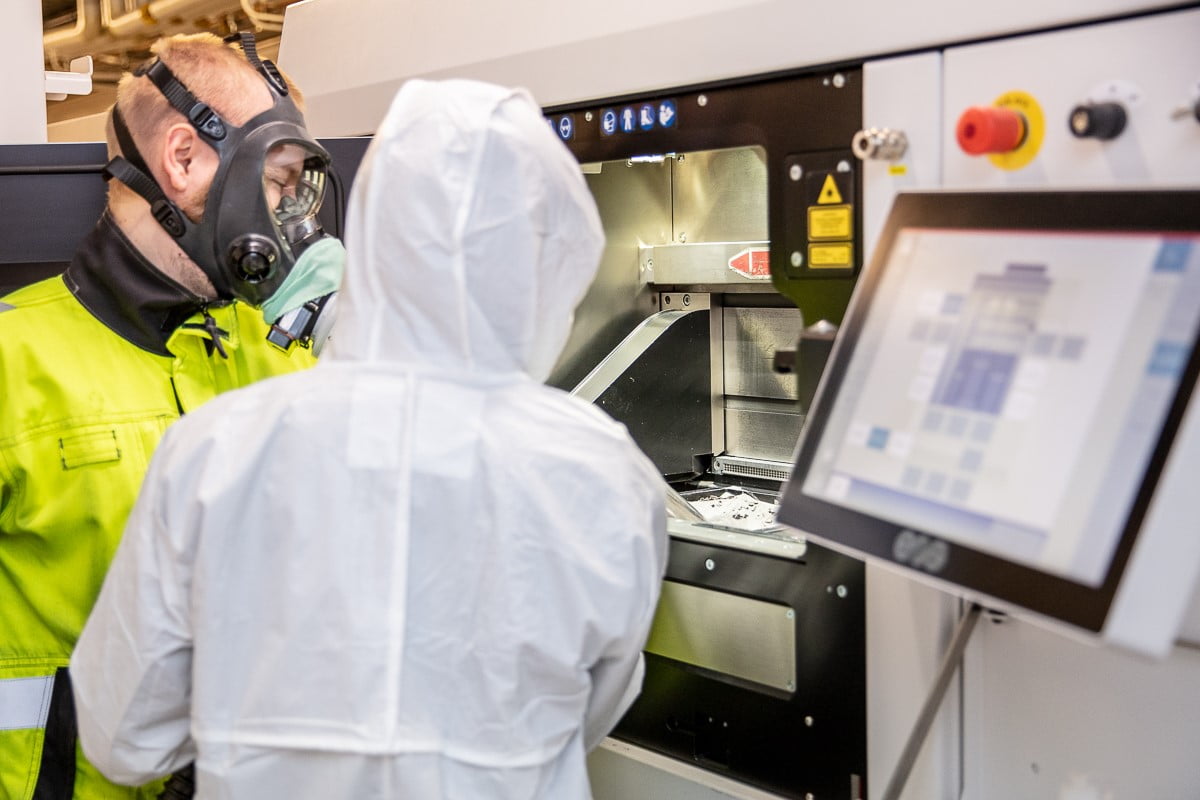
Picture: The build is ready.
Economic view to metal 3D-printing
Delva talks about the significance of material selection to gain maximum benefits. Openness to new materials that metal printing enables is far-reaching. Stick to old holds back the development.
It is essential to have also the economic view: familiarising with the production makes it evident how each new material requires significant investments in powder handling, the powder itself, and printer parameters. Every material also demands material-specific know-how. We need volumes to implement all this. Also, the efficiency of the printing process increases when the material-specific building plates are as tight fulfilled as possible, which brings the customer a cost advantage. Due to the reasons mentioned above, a more profound understanding of various printable materials and their usability benefit all. Trust and encouragement to choose something differing from earlier are bolstered by shared experiences and success stories.
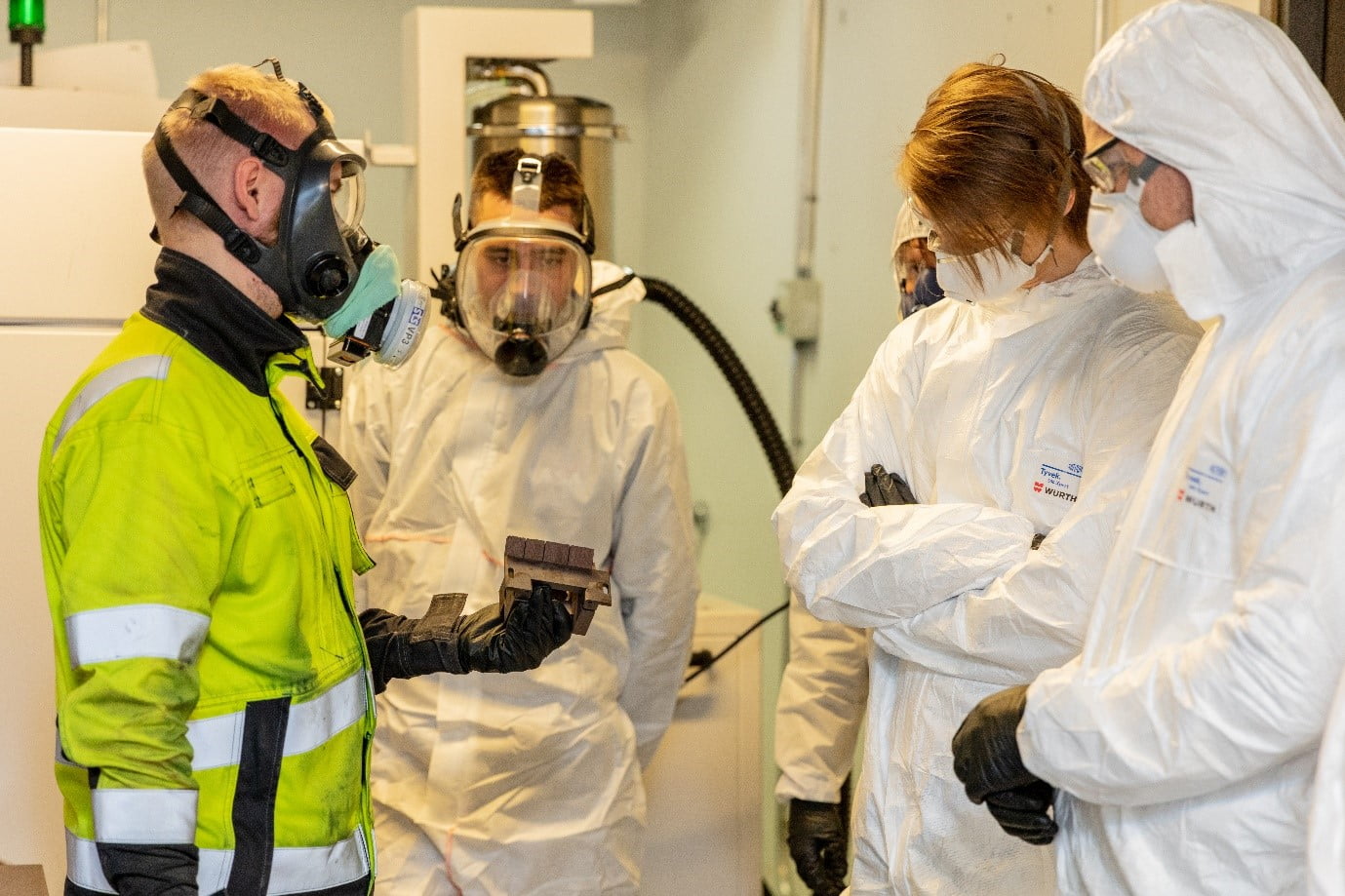
Picture: The protective set-up reminds us of the fineness of the powder that exceeds wheat flour. Protection is a must.
Is this something for your company?
We want to thank all the participants at metal printing days and are happy to continue cooperation. As stated many times before, cooperation is a strength.
If you are interested in organising a similar day for your organisation, please, contact us. Let us build a program that best supports your target setting.
The picture on the top of the page: Personnel from FAME member companies familiarising with metal 3D printing at Delva Oy in Hämeenlinna in January 2022. Delva´s CTO Markku Lindqvist is explaining.
Contact and more information:
marja-leena.makinen@delva.fi, +358 50 431 7034
Pictures: Valokuvaus Viirukka