We at Delva want to emphasise that Inconel 718, Inconel 625 and HX, all nickel alloys, are relevant alternatives for stainless steel as certain central features achieved with Inconel are better than with 316L.
In the latter chapters, we will also discuss Inconel 939, the royal of the Inconel superalloys.
The Inconels are great examples of materials worth thinking outside the box.
Inconels’ performance values
The yield strength of Inconel 718 is around 1200 MPa, Inconel 625 has a yield strength value of 650 MPa, while 316L has only 250 MP.
Pitting resistance equivalent numbers (PRE-numbers) are often used for stainless steels to determine resistance to pitting corrosion. The trait has its base on its chemical composition. Generally, the higher the number, the better an alloy’s corrosion resistance in chloride solutions.
The PRE-number for corrosion resistance is 52 for both Inconel 625 and HX, 29 for Inconel 718, and 26 for stainless 316L.
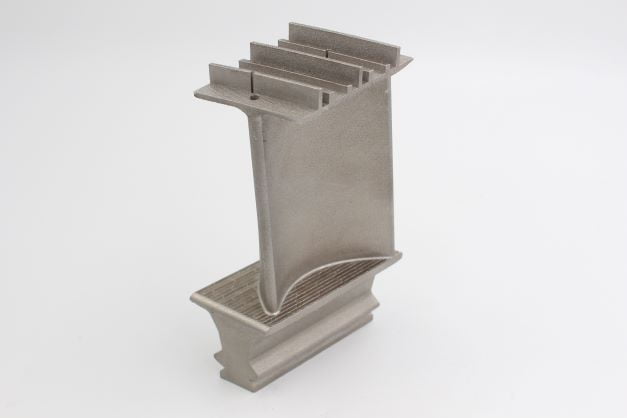
Cost-benefits using Inconel
The costs of using these Inconel superalloys are similar to stainless steel, even lower when exploiting the materials’ advantages. The better performance allows us to design lighter structures, which means less printed material and less cost.
The durability of Inconel is outstanding. That prolongs the lifetime, and that way lowers costs further.
Inconel and conventional manufacturing methods
The parts printed from Inconel 718 are nearly 100% dense and have the same material characteristics as conventionally manufactured Inconel parts.
Inconel is known for its somewhat challenging weldability. Delva has ongoing collaborative research to further research weldability, especially in dissimilar material pairs. Improved weldability enables joining superalloys with other, more conventional materials. For example, you can have a base structure using 316L, print the part with critical properties with Inconel, and join these two by welding.
Depending on the Inconel class, neither is the machining straightforward. Generally, the printing of Inconel reduces the need for machining as the pieces are often good enough as printed. But there are always certain areas like sealing surfaces and others that need to be machined. For that, knowledgeable machinists and available processes are essential assets.
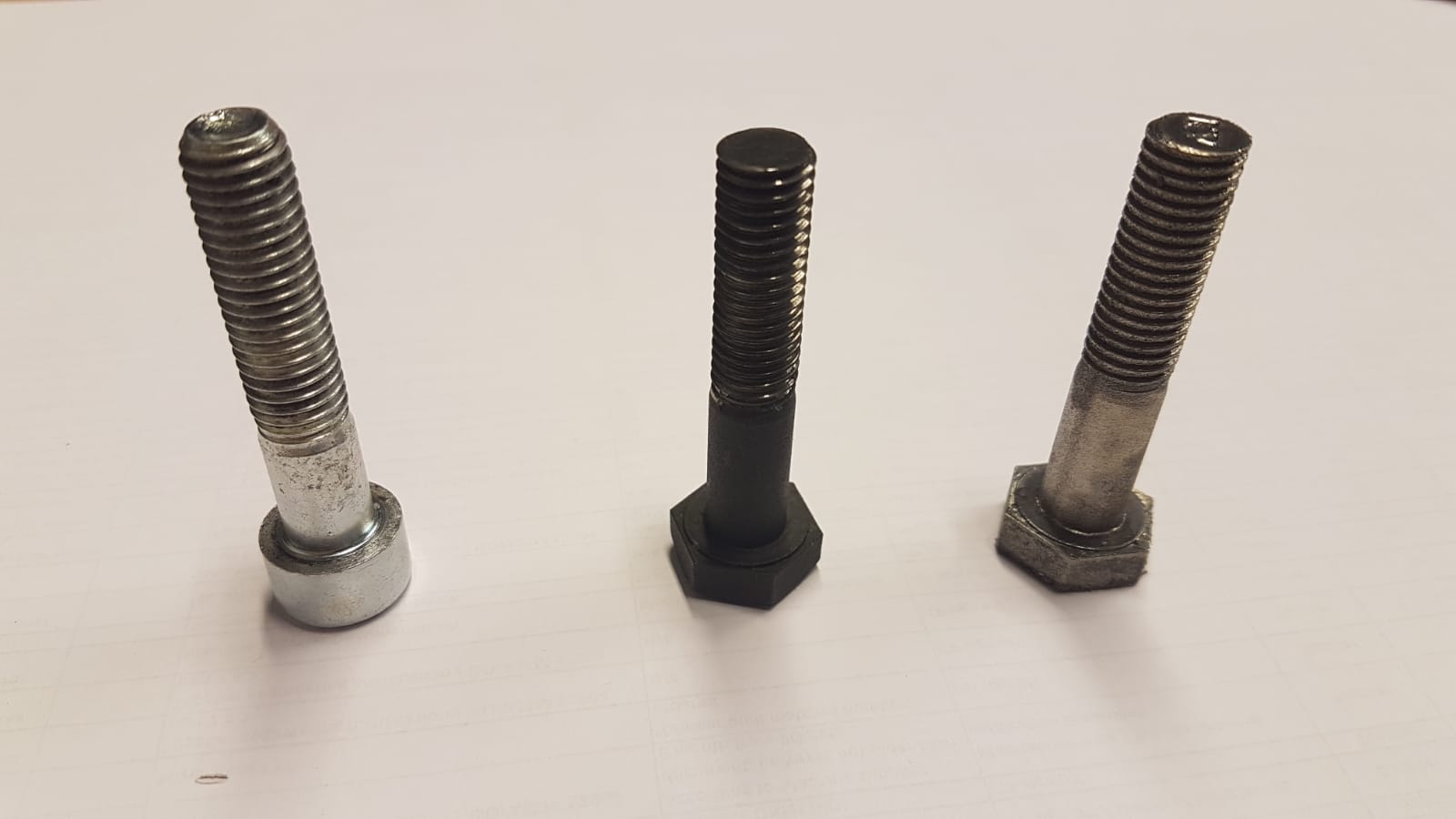
Testing Inconel 718
Delva has earlier printed threads from Inconel 718 for tensile testing, with outstanding results.
The quality of threads was excellent, and tensile testing showed: strong – stronger – 3D printed Inconel.
Recently, a master thesis on the fatigue properties of Inconel 718 and the effect of heat treatment on the properties took place at Delva.
Fatigue strength is generally recognised as a critical property in industrial applications and needs to be studied carefully. On the other hand, heat treatment is a way to modify material properties like hardness. It is essential to be aware of how heat treatment affects on fatigue strength of the material, in this case, Inconel.
The tests showed the consistently high quality of the fabricated Inconel 718 material with a predictable response to cyclic stress at different amplitudes. The study’s results supported the effort to develop tailored material properties for industrial applications using modified heat treatments. Further extensive testing will take place, but initial results were already encouraging; according to the result curves, the material whose properties we altered by non-standard heat treatment meets the requirements in terms of dynamic load.
The royal of superalloys, IN939
Some time ago, EOS introduced a new nickel-based alloy, EOS NickelAlloy IN939, for additive manufacturing.
Thanks to its excellent oxidation resistance and outstanding mechanical properties at elevated temperatures, IN939 opens new possibilities for additive manufacturing in demanding applications. EOS NickelAlloy IN939 offers improved temperature capabilities and excellent mechanical properties up to 850 °C, which is 200 °C more than IN718.
IN939 is a crack-free, strain-age-resistant product. Having an optimised heat treatment without requiring HIP (Hot Isostatic Pressing) significantly reduces post-treatment costs and effort.
During the development of IN939 , EOS has worked in engineering and heat treatment, while Delva has advanced machining and welding process development with its specialist network.
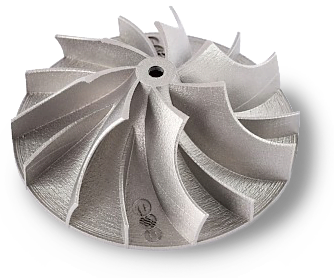
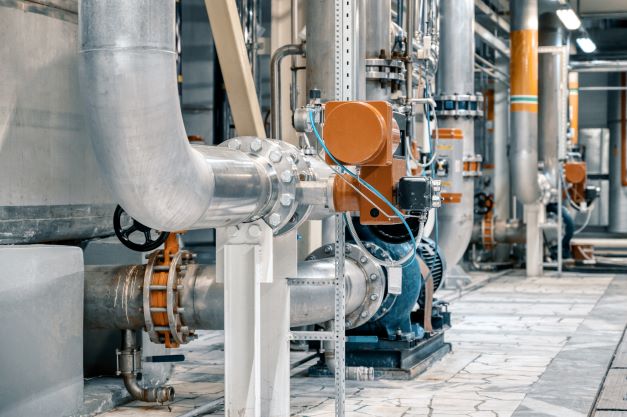
Ready materials for demanding applications
The printable Inconel materials available from us are
EOS NickelAlloy IN718,
EOS NickelAlloy IN625,
EOS NickelAlloy IN939 and
EOS NickelAlloy HX.
Together they are suitable for an extensive range of applications.
Thanks to IN939, potential applications include stationary gas turbine industries and applications like guide vanes and heat shields. Previously existing materials designed for additive manufacturing have not been suitable for such applications.
Following Delva’s philosophy, Delva serves customers in the way that best fits the customer’s needs. That includes even Inconel 939 parts being available as ready-machined parts from Delva.
For more information:
CTO Markku Lindqvist,
+356 50 522 5016
markku.lindqvist@delva.fi,
info@delva.fi