As an integral part of the manufacturing methods, metal printing creates new opportunities. It allows us to go further with less and smarter. Snowsus achieved this when it used metal printing for its advanced suspension solution. It is essential to think carefully about the structure you want to achieve and the material in metal printing. With the right choice of material, we can multiply the benefits of printing.
The trend towards electrification creates a need for new solutions
In mobile solutions, weight plays a significant role. Metal printing is an enabler here too. Particularly with electrification, mass is becoming increasingly important; we have to compensate for the extra weight of batteries and other electrical components by reducing the weight of other elements. This is also one of the core themes of Snowsus’ new solution: the range of electrically powered equipment is proportional to its weight and the capacity of the batteries. In lightweight off-road vehicles, weight reduction naturally makes sense and is also relevant to environmental impact.
Snowsus innovates
Snowsus Ltd is a company developing a new and patented snowmobile suspension system. It is a powerhouse of new solutions and has innovated a lighter suspension solution. This solution significantly benefits ecology, driving comfort and life cycle costs. The company recognised the potential of metal printing as a solution. To lighten the snowmobile suspension, it explored the use of metal printing in manufacturing components.
Snowsus chose Delva as its partner for the project. “We chose Delva because the company’s experts in metal printing are of a high level. In addition, Delva has the widest range of materials at its disposal so that we can test different materials at different stages of the project,” says Timo Kronqvist, Snowsus CEO and board member.
Together, the companies honed a visually stunning component optimised for weight and strength into a suspension system.
“The material chosen for the component in the first phase of the project was tool steel MS1, a strong and relatively inexpensive material that, in this case, provided the basis for evaluating the functionality of the solution and is also easy to weld to other structures. In the next phase, it will be possible to lighten the solution with other materials such as titanium. By exploiting the strength properties of titanium, we can build the solution cost-effectively and reduce the mass of suspension even further,” says Kronqvist.
Making the most of materials is also encouraged by Markku Lindqvist, Technical Director at Delva: “When choosing materials, it is worth breaking away from the familiar and exploring the alternatives that printing offers. Let’s start with the purpose and the goal and choose the material based on that. The purpose and objectives may differ at different stages of a development project, as in the case of Snowsus. We can help your company with its considerations.” For more ideas on material choices, see Delva’s Printing Materials Guide
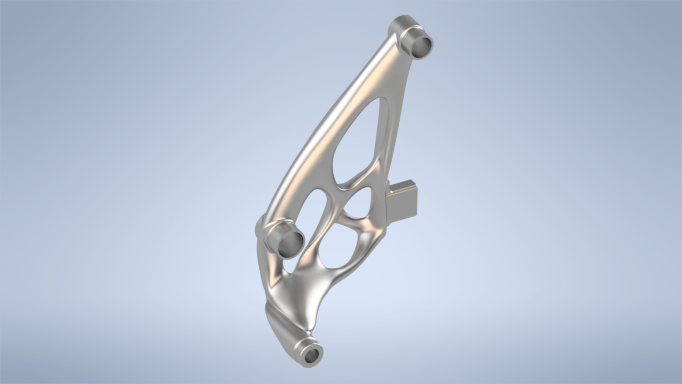
The customer is an expert in his field, Delva master in printing
A new printing component contributes to a significant reduction in the weight of a snowmobile suspension. “The cooperation with Delva went very well. We knew what we were looking for in a solution; Delva knows printing,” says Kronqvist.
Delva’s Lindqvist has nothing but excellent co-development experience with different customer companies. “We at Delva offer exactly the partnership the customer needs. The customer has the best knowledge of the industry, its solutions and the company’s vision, and the experience of the processes. These are the core competencies of each company”.
“In the design of 3D printed parts, on the other hand, specific know-how is needed to take advantage of the laws of 3D printing on the one hand and to take account of the limitations on the other. Printing and materials are strongly interlinked areas of expertise, requiring both skill and experience. Each material has characteristics that must be considered to achieve a successful result. In addition, a deep knowledge of simulation, optimisation, calculation, post-processing, etc., is required. This is where we offer our support,” Lindqvist continues.
Read more about our ideas for a partnership in metal printing here.
Snowsus as a guest at the Pohjoinen Teollisuus event
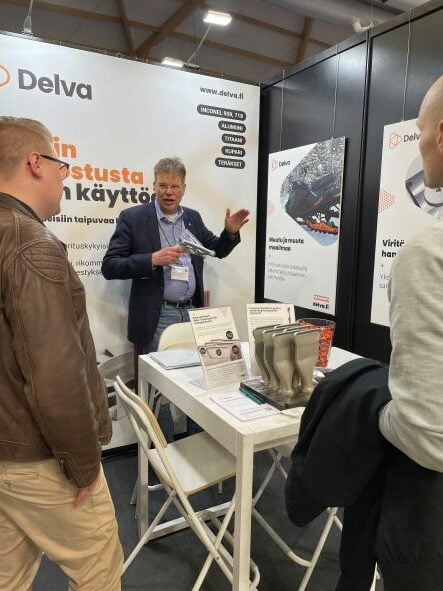
Snowsus’ Timo Kronqvist was Delva’s guest at the Northern Industry event on 17 May 2022. Timo told his snowmobile enthusiast audience about Snowsus’ revolutionary, patented solution: “that does not resist force, but adapts and redirects it”. The spearhead of the design is a highly lightweight rear suspension that offers a power-to-weight ratio in a class of its own. The wear in the solution is in a class of its own and reduces life cycle costs. Even belt tension in all conditions contributes to reduced friction and extended range. Overall, the Snowsus solution is lighter and more stable to handle than conventional solutions.
Forerunners expand their range of options
At Delva, we are firmly convinced that the best way for the industry to benefit from metal printing is to make it an integral part of its tool portfolio. Then its potential is recognised in all aspects of a company’s operations: in the development of production processes, in maintenance opportunities, in taking machinery and equipment to a new level, and in the potential to create entirely new business.
Snowsus is a pioneer with its innovative suspension solution. Metal printing extends its range of tools and helps realise the solution from the goal and purpose. This is an example to keep in mind. Get in touch with Delva when you are considering developing your business.