The heavy industry process was made more efficient while the need for spare parts and maintenance was reduced with a more durable component printed from Inconel.
A company that develops suspension systems for vehicles took the lead by lightening its solution with a topology-optimised metal print.
The machine builder’s product development takes advantage of prototypes’ 3D print-enabled mass production. The approach shortens the testing phase and saves costs.
The manufacturing company gained more years of operation for its ageing equipment and reduced production downtime by printing a spare part.
The above examples are just the tip of the iceberg. Metal printing is an enabler in many situations. Integrating metal printing into every company’s range of manufacturing methods makes sense. Delva is your flexible partner in the use of metal printing.
The use of metal printing in the industry is growing rapidly, but companies have publicly opened up very little about their development projects. After all, this is easy to understand as the goals are often strategic, and successes provide a sustainable competitive advantage. The actors who have presented their encouraging experiences deserve a big thank you, as they are leading the Finnish industry by leaps and bounds by example.
Either-or or both-and?
Will the lights soon go out in the foundries and the work in the machine shops stop when orders are transferred to the printing service bureaus’ 24/7 unmanned machine shops? Will customers soon be printing the equipment and spare parts they need themselves? Will steel mills switch their continuous casting processes to atomisation and the supply of steel bars to powder bins? These utopias – or perhaps, for some of us, dystopias – are unlikely to come true in our lifetime. But change is happening. Instead of either-or, it is both-and, according to Delva.
At Delva, we believe that the best way is to integrate metal printing into the range of utilised manufacturing methods. Then its potential is recognised in all aspects of a company’s operations: in the development of production processes, in maintenance opportunities, in taking machinery and equipment to a new level, and in the possibility of creating entirely new business.
However, printing does not replace more conventional manufacturing methods but complements them. Printing removes manufacturing limitations and opens up new design possibilities with purpose and purpose only in mind. It makes it profitable to use new, previously expensive or otherwise tricky materials to exploit. It helps create something unique with less and more wisely and therefore sustainably. However, metal printing may need, for example, machining of the sealing surface or other features produced by a more conventional manufacturing process. At the same time, many components are not economically viable or cannot be printed due to manufacturing constraints such as size. Therefore, it is a skill and a prerequisite for success to exploit the full range of expanded manufacturing possibilities.
The right choice of materials multiplies the benefits
Mechanical engineering has become accustomed to using particular materials because they are perceived to offer adequate performance and cost-effectiveness for their applications. Changing the material can seem like a chore. However, sticking with the same old materials for printing also leads to compromises that do not achieve the best possible benefits. It should also be noted that not all familiar materials are even available in the printing material range, as it does not make sense to print them. Therefore, new materials need to be explored; they will bring results.
An excellent example of the possibilities opened up by metal printing is Inconel. It is a corrosion-resistant nickel alloy that is very strong even under extreme conditions. Inconel is available in different alloys, such as Inconel 718 (IN718), Inconel 625 (IN625) and Inconel 939 (IN939). Each of these has its characteristics and applications. They have in common that they are heat resistant and therefore suitable for demanding applications. Although Inconel has many advantages over stainless steel in terms of performance, its use has so far been limited. This is mainly due to its challenging machinability due to hardening. Printing has the potential to change this situation.
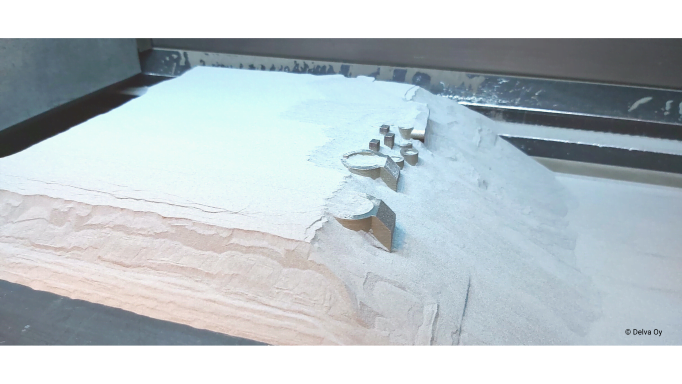
Photo: Laser Powder Bed Fusion (L-PBF) is the most advanced metal printing technology and produces components for the most demanding industrial applications.
The dimensions of knowledge in metal printing
Metal printing is an opportunity that permeates the entire company. Developing a broad range of skills is essential to take advantage of the opportunities. It is crucial to identify how different functions could benefit from metal printing. Productivity, competitiveness, and sustainability are jointly underlined by the industry and where printing opens new possibilities.
It is good to identify the different areas of competence and consider how to achieve an adequate level in each aspect. A key area of competence relates to knowledge of one’s industry, solutions and visions for the industry, processes, and basic rules in production. These are the core competencies of each company.
Specific skills are needed in designing printed components to exploit the rules of printing and optimise the parts while taking account of the constraints. Printing itself and materials are strongly interlinked areas of expertise, requiring both skill and experience. Each material has its characteristics, which must be considered to achieve a successful result. In addition to all this, a deep knowledge of simulation, optimisation, calculation, post-processing, etc., is required. Each company chooses its 3D printing path and sets its targets.
Getting the most out of digital manufacturing
Most companies have set targets for this trajectory: Digitisation, digitalisation, and digital transformation. The opportunity to increase productivity is obvious but requires significant investment.
3D printing is inherently digital manufacturing and always requires 3D models of the parts to be produced. Software development around printing has been massive in recent years. Tools are available for design support, efficient production planning, control, and continuous production monitoring.
Print simulation is a significant aid for challenging structures, which helps anticipate and compensate for heat-induced deformations in the manufacturing process. The printed part conforms to the design. Delva uses simulation to help companies achieve a successful outcome more straightforwardly.
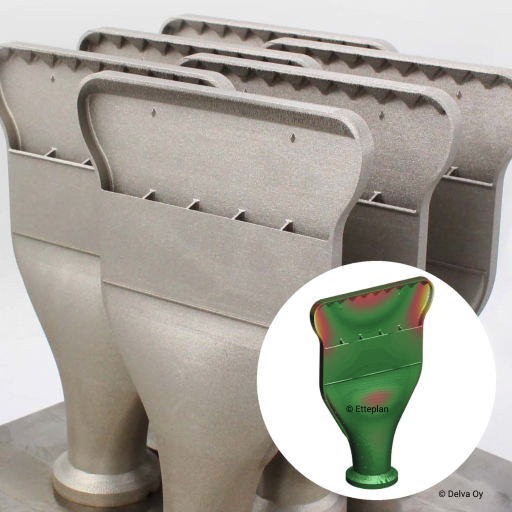
Photo: In challenging structures, print simulation helps anticipate and compensate for heat-induced deformations in the manufacturing process.
Partner the way you want
Successful companies look for ways to succeed, and at Delva, we remind you that you don’t have to know or have time to do everything yourself. The same applies to the investments in printers and equipment significant in metal printing. The pace of development in metal printing is fast, and even keeping up with the latest developments requires resources. You can also benefit from this development with smaller and more predictable investments. This is where the use of existing know-how is often a good solution.
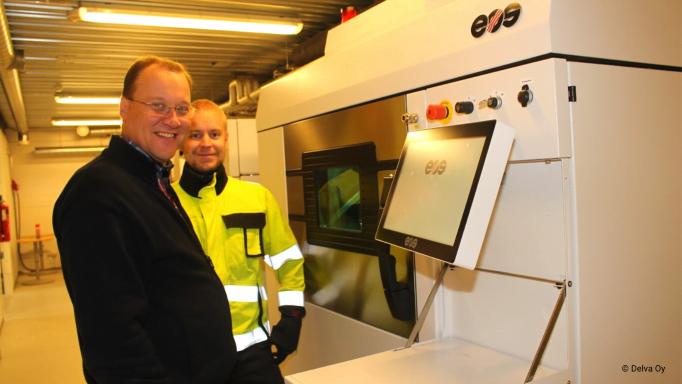
Photo: Delva is a competent metal printing partner for the industry. CEO Jarmo Kastell (left) and CTO Markku Lindqvist encourage the industry to take advantage of the opportunities offered by 3D printing.
At Delva, we offer a partnership that adapts to our customers’ needs. Needs can be far-reaching development partnerships, new creation and knowledge building, pure 3D printing capacity, or combination. The client decides the level of collaboration. For us, metal printing in Delva is a source of inspiration and a sea of opportunities. We learn and teach. We develop and print. We offer the broadest range of materials in metal printing in Finland, from Inconel to titanium and from tool steel to copper. We do it all with a pro-industry attitude and know-how. So come and challenge us. We print any part*) *) within reason, of course.
Comments and more information: marja-leena.makinen@delva.fi.
The article was at the first time published in Eurometalli 02 2022.