Industrial applications typically require high-performance components. In some cases, the classic combination of material properties is not enough; a specific property can be necessary. Altering the properties of 3D-printed materials to customise their performance for their intended applications is doable. Goal orientation requires careful consideration.
Industrial applications typically require high-performance components. The properties of metal prints are at the same level as conventionally produced parts, often even better. The combination of high-quality powders and 3D printers and the parameters designed for these two produce uniform, reliable, and repeatable components.
“In some cases, the classic combination of material properties is not enough; a specific property can be required instead.”
In some cases, the classic combination of material properties is not enough; a specific property can be required instead. Ready solutions seldom exist, but the situation can be solved based on theoretical evaluation, realisation based on it, and, eventually, comprehensive testing. However, a process change can have broader implications for the material. Curiosity must go hand in hand with responsibility.
We at Delva have researched, tested, and found it possible to use different heat treatments to alter the properties of 3D-printed materials to customise their performance for their intended applications.
Curiosity and customer needs drive our research
The dynamic fatigue life of parts is critical for many industrial applications. Even though the practical experiences are good for metal 3D printed parts, the academic research and data have been somewhat narrow. This is the case for Inconel 718, a nickel superalloy, which offers a robust, corrosion and wear-resistant alternative for various industrial applications. The research field needed replenishing.
In specific industries, such as oil and gas, Inconel is an advantageous material. However, some usually desirable material properties might not be suitable for the industry’s standards and can limit the use of these materials. With the identified general need and an interesting industry case in mind, we set out to modify Inconel in a softer direction through heat treatment. It was necessary to do this without jeopardising the fatigue life.
As a result, we raised the question of the fatigue life of Inconel 718 after application-specific heat treatment and how it differs from the material with standard heat treatment.
The material meets the requirements
To contribute to research on these crucial topics and also to benefit the usage of 3D printed Inconel in the named industry, Delva initiated a master’s thesis. The title “Study on the fatigue properties of Inconel 718 and the effect of heat treatment on the properties” speaks for itself. Mikko Paavilainen from Tampere University conducted the research study, and Professor Pasi Peura and Delva CTO Markku Lindqvist guided the project.
Markku Lindqvist is satisfied with the results of the study. The tests showed the consistently high quality of the fabricated Inconel 718 material with a predictable response to cyclic stress at different amplitudes.
Markku also emphasises the results supporting the determined effort to develop tailored material properties for industrial applications using modified heat treatments. Further extensive testing will take place, but initial results are encouraging; according to the result curves, the material whose properties we altered by non-standard heat treatment meets the requirements in terms of dynamic load.
In the following, Mikko Paavilainen discusses the study, its central findings and the conclusions.
We thank Mikko for his excellent cooperation, dedication, and determined work to foster the utilisation of metal AM in industrial applications.
Study on the fatigue properties of Inconel 718 and the effect of heat treatment on the properties
by Mikko Paavilainen
Due to the complexity of the metal additive processes, it is vital for a company operating in the field to not only understand the process and related parameters but also understand the materials they are working with, as well as the effects different post-processing treatments have. Compared to manufacturing methods such as casting, an increased responsibility is shifted onto AM parts’ fabricators.
For this work, the main interest was directed towards the fatigue properties of the Inconel 718 superalloy, more specifically, the effect of heat treatment on as-built material under cyclic stress and the differences in corresponding fatigue life.
To keep the resources spent on the experiments to a reasonable level, it was agreed that a single patch of identical samples was fabricated using EOS M290 with standard EOS process parameters. The built samples were split into two groups, each receiving a different heat treatment procedure. The other group was treated with EOS-recommended treatment, while the other received a novel treatment.
One of the goals of the novel treatment was to reduce surface hardness. That can compromise some mechanical properties, but in this case, the point of interest was fatigue life.
It was also in the interest of the experiments to use an as-built surface, which can severely compromise the fatigue properties of metal materials due to the increased number of areas of concentrated stress. That is particularly the case with AM-fabricated parts due to limited control of the melt pool dynamics on the outermost edge of the build layer.
The surface quality can often be relatively easily improved in more simple parts that do not contain hollow structures or complex internal channels. If those inaccessible features are included, the operations for refining the inner surfaces can be difficult and expensive. So, it is highly beneficial to understand the material behaviour under suboptimal conditions. The building that understanding is the reasoning behind the choice of using untreated surface quality in these experiments.
Experiments and findings
The fatigue tests were performed on Tampere University Hervanta campus using MTS 810 servo-hydraulic test device. First, the ultimate tensile strength (UTS) was assessed to set a standard for the upcoming fatigue testing, with the value coming in at roughly 1350 MPa. The fatigue tests were then carried out at specific fractions of the UTS using a tensile-tensile procedure with a load ratio R of 0.1.
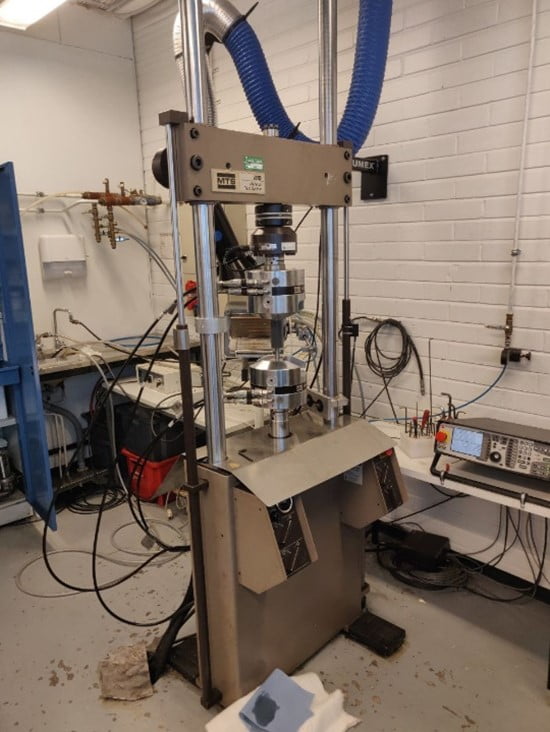
MTS 810 Test device.
The results of the fatigue tests proved interesting. The reference heat-treated Inconel 718 exhibited significantly better fatigue life when subjected to high-stress amplitudes, with Nf more than double the novel treatment. At lower stress amplitudes, though, the novel treatment invariably showed improved fatigue life compared to the reference. The point at which the two treatments are equal in terms of fatigue life is around a stress amplitude of 700 MPa.
Also worth noting is the conformity of the results was surprising. With fatigue being a probabilistic phenomenon and using untreated surface quality, the expectation was for a notable amount of variance in the observed fatigue lives. But all results lined up very close to a predictable line with high R2 values. Recognising the relatively small sample size is important, making the findings promising but not definitive.
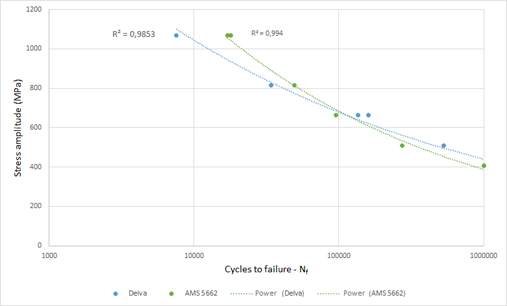
Fatigue test S-N curves and R2 values.
If conclusions about the material quality had to be based solely on the fatigue life values, then the results would indicate good things. Combined with the images obtained with scanning electron microscopy (SEM), the material structure and consistency are desirable. The images showed a microstructure typical of AM fabricated metal material, with a melt pool path heavily affecting the solidification of the grains. In higher magnification, the structure really exhibited high levels of homogeneity. Moreover, there was very little in the way of finding defects. The porosity which could be observed was sized in the range of a micron or so.
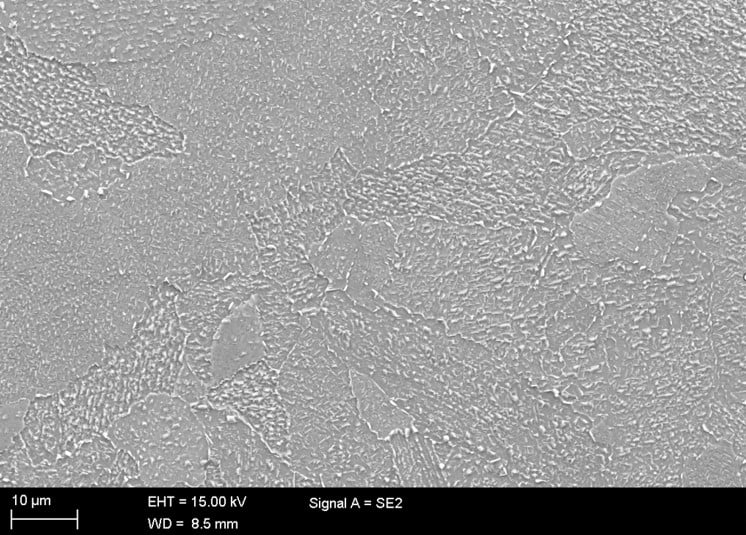
SEM image of the Inconel 718-grain structure in a sample subjected to the novel heat treatment.
Conclusions
Due to multiple variables significantly affecting the results, direct comparison to other studies can be difficult when analysing fatigue life. In this case, the point of the study wasn’t to prove the superiority of the mechanical properties of the fabricated objects, hence the use of an as-built surface, but to understand the material better.
In this regard, the experiment worked out well. The tests showed the consistently high quality of the fabricated Inconel 718 material with a predictable response to cyclic stress at different amplitudes. The effect of the heat treatment proved to be notable and worth investigating. The novel treatment didn’t obsolete the reference treatment but showed desirable properties for some applications.
So, in this case, if used in engineering applications, it would be up to the design and use environment of the particular component whether the new treatment would be preferable. Overall, the fatigue properties of all fabricated samples were in line with expectations for such material. The novel heat treatment performed well and reached the objective. For certain types of use cases, it displays promising attributes. To advance into full-scale utilisation of the heat treatment, performing more wide-scale mechanical testing would help to ensure other properties are not severely compromised. That was beyond the scope of this study.
Regarding the as-built surface quality, the object was to evaluate whether the untreated material surface proved viable for use. While it is undoubtedly beneficial to minimise surface roughness, the observed predictability in the fatigue life experiments supports the conclusion that the as-built surface will suffice in some cases, even when subjected to cyclic loading. These cases are mainly those in which it is possible to use a design that keeps stress concentrations to a reasonable level, typically compromising on things such as weight.